ExxonMobil provides guidance for on-board grease changeovers
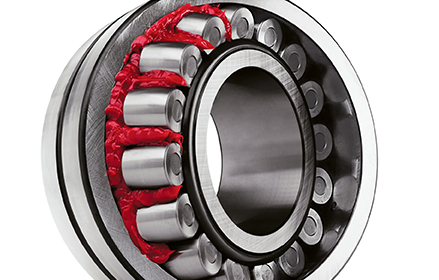
Mixing greases, even those with similar types of thickener, can lead to ineffective lubrication. In turn, this can result in component damage and ultimately lead to equipment failure. It is therefore important that vessel operators understand the issues when switching and how best to avoid them.
Compatibility issues
One of the most frequent incompatibility problems is a change in consistency relative to the individual greases in a blend. This becomes more pronounced as the operating temperature or the shearing rate of the grease mixture increases.
Incompatible greases can display abnormal oil separation or “bleeding” at higher temperatures. This can be so severe that the mixed grease will run out of an operating bearing resulting in catastrophic lubrication failure.
Compatibility cannot be predicted with any certainty and should therefore be judged on a case-by-case basis. Importantly, conditions such as temperature, shear rates, the state of the used grease replaced and the ratio of the greases in the mixture can all affect compatibility.
Laboratory testing
Industry standard ASTM D6185 sets out practices for evaluating the compatibility of greases by comparing the properties or performance of the blend against those of the greases comprising the mixture. Typically the constituent greases are blended in two ratios: a 50:50 mixture simulates a ratio that might be experienced when no attempt is made to flush out the old grease, while 10:90 and 90:10 ratios simulate when grease flushing has been attempted.
Best practice
Equipment manufacturers recommend completely cleaning grease from equipment before installing a different product. However, there are times when mixing cannot be avoided. Under those circumstances compatibility testing is strongly advised.